The Cost of Inefficiency: Why Crushers Matter
According to the Global Aggregates Association (2024), 23% of operational costs in quarries stem from inefficient crushing processes. Outdated equipment leads to:
⚠️ Energy waste: Up to 35% higher power consumption
⚠️ Material loss: 10-15% of product becomes unmarketable fines
⚠️ Downtime: 120+ hours/year lost to maintenance
Modern stone crushers address these challenges through 6 key innovations.
Strategy 1: Energy-Saving Designs Cut Power Costs by 40%
Comparative Energy Consumption (kWh/ton):
Crusher Type | Traditional Model | 2024 Eco-Smart Models |
Jaw Crusher | 1.8 | 1.1 (e.g., Sandvik CJ615) |
Cone Crusher | 2.4 | 1.5 (e.g., Metso MX4) |
Impact Crusher | 2.0 | 1.3 (e.g., Kleemann MR 130i) |
Technology Spotlight:
- Hybrid Power Systems: Caterpillar’s C3.8 Tier 4 engines slash fuel use by 28%
- Variable Frequency Drives (VFD): Adjust motor speed based on load, saving 15-25% energy
Strategy 2: Smart Automation Reduces Downtime by 60%
AI-Driven Predictive Maintenance Systems:
- Real-Time Monitoring: Track 50+ parameters (bearing temp, vibration, pressure)
- Failure Prediction: Alert operators 72 hours before breakdowns (e.g., Siemens SIMINE Crusher)
- Case Study: A Turkish quarry extended crusher lifespan by 18 months using Metso Metrics
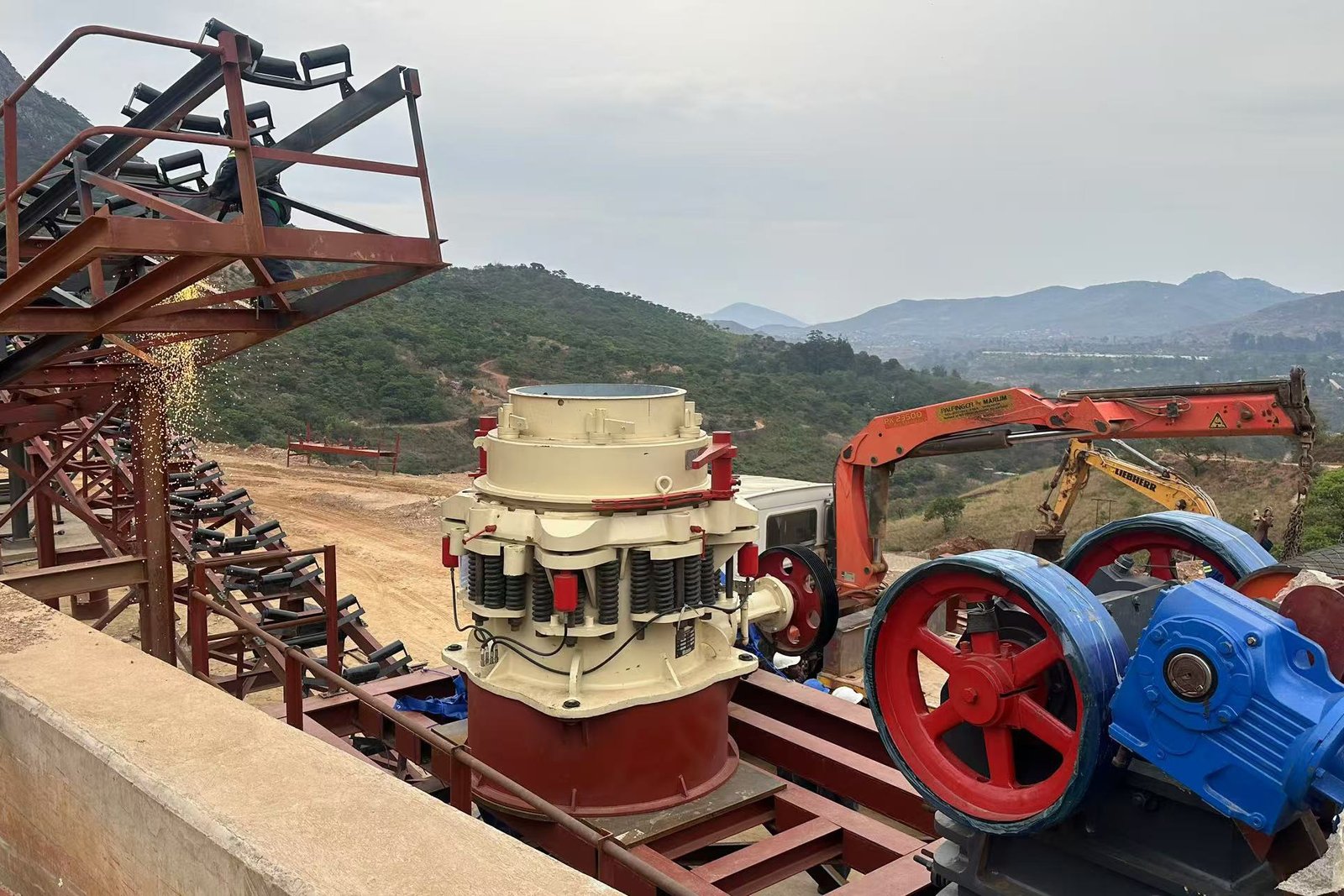
Strategy 3: Multi-Stage Crushing Boosts Yield by 30%
Optimal Configuration for Granite Processing:
Stage | Crusher Type | Feed Size (mm) | Output (mm) | Purpose |
1 | Gyratory Crusher | 1065-1525 | 250 | Primary reduction |
2 | Cone Crusher | 35-460 | 50 | Secondary shaping |
3 | Vertical Shaft Impact Crusher | 37-50 | 8 | Cubic final product |
Result: 98% usable aggregates vs. 82% with single-stage crushing.
Strategy 4: Modular Designs Cut Installation Time by 75%
Mobile vs. Stationary Crushers:
Factor | Mobile Crusher (e.g., Lokotrack LT120) | Traditional Stationary Plant |
Setup Time | 2-4 hours | 3-6 weeks |
Relocation Cost | $5,000 | $80,000+ |
Ideal For | Multi-site contractors | Large fixed quarries |
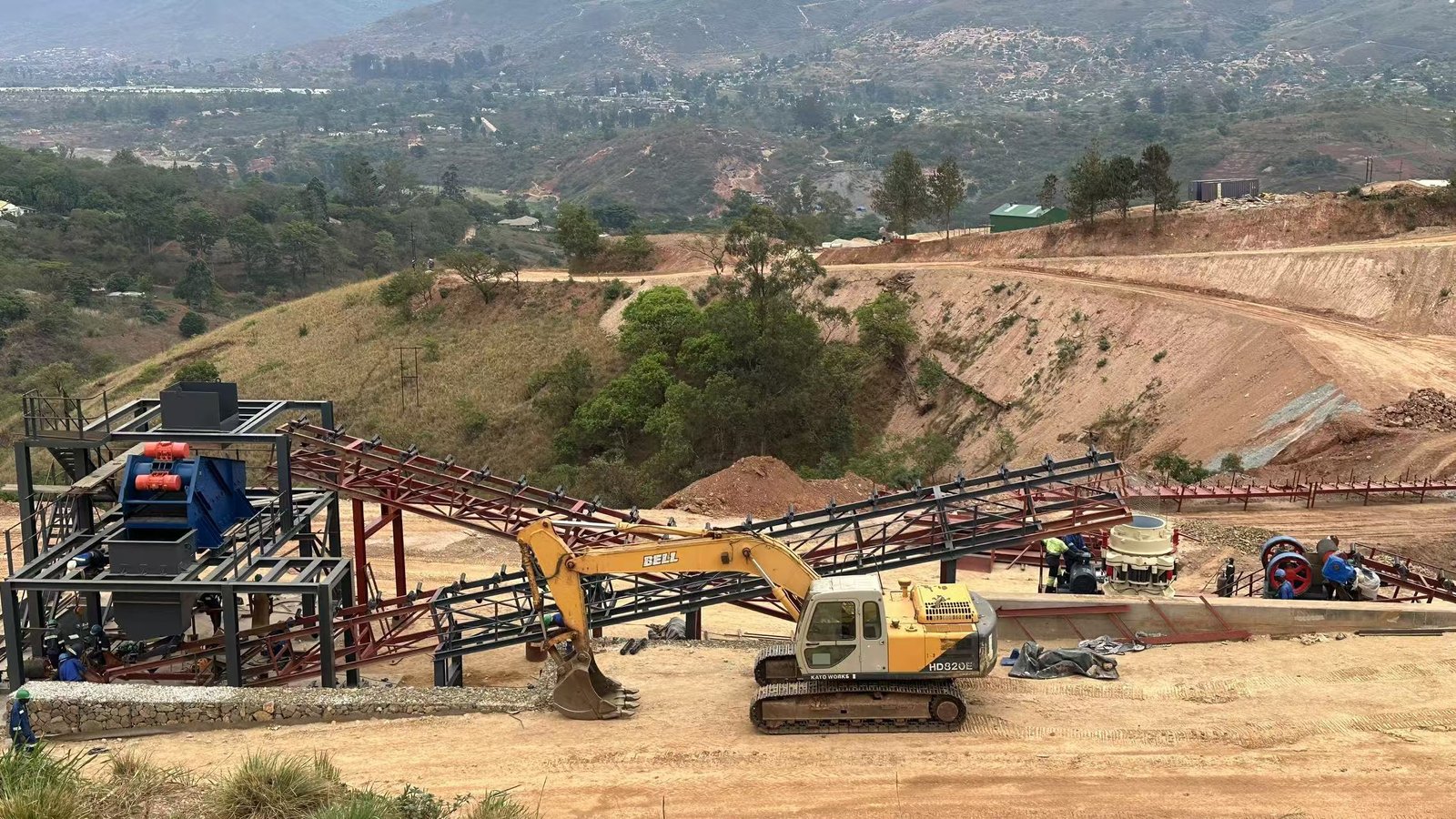
Strategy 5: Advanced Wear Parts Extend Service Life by 2X
Material Breakthroughs:
- Ceramic-Infused Liners: Resist abrasion in high-silica rocks (6,000+ hours lifespan)
- 3D-Printed Hammers: Custom geometry for specific materials (e.g., FLSmidth’s HYDRARAM)
- Self-Sharpening Blades: Maintain edge through 800+ operating hours
Strategy 6: IoT Integration for Real-Time Optimization
Smart Crusher Ecosystem:
Sample Caption: IoT sensors feed data to centralized dashboards enabling instant adjustments
Key Metrics Tracked:
- Throughput Rate: Compare actual vs. target (e.g., 550 tph vs. 600 tph)
- Power Usage per Ton: Alert when exceeding baseline by 15%
Wear Part Efficiency: Schedule replacements at 85% wear level
ROI Calculation: How Much Can You Save?
Input Your Numbers:
Parameter | Your Value | Industry Avg. |
Daily Production (tons) | _________ | 5,000 |
Current Energy Cost/ton ($) | _________ | 2.10 |
Annual Downtime (hours) | _________ | 150 |
Potential Savings with Upgraded Crushers:
- Energy: $______ /year (40% reduction)
- Labor: $______ /year (automation cuts staffing needs)
- Maintenance: $______ /year (predictive systems reduce parts replacement)
Future Trends: What’s Next in Crusher Efficiency?
- Hydrogen-Powered Crushers: Volvo CE prototypes target 100% emission-free operation by 2026
- Blockchain Material Tracking: RFID-tagged aggregates for quality assurance (BHP pilot)
- AR Maintenance Guides: Overlay repair instructions via smart glasses (Komatsu’s SiteVision)
- Ready to Transform Your Operations?
- Book a free efficiency audit with our engineers to:
- Analyze your current crushing workflow
- Identify 3-5 priority upgrades
- Access exclusive OEM financing options